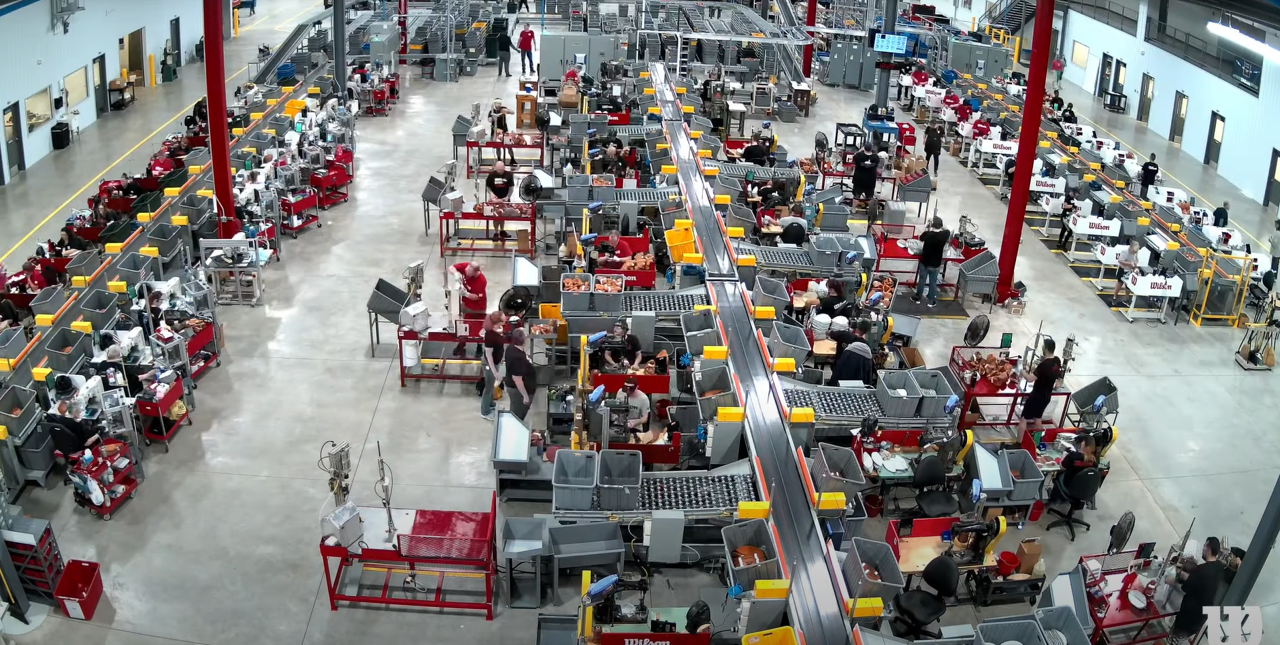
A team of 140 union-represented factory workers make footballs by hand in Ada, Ohio, the small town that Wilson has called home since 1955.
Are you ready for some football?
The National Football League (NFL) kicks off Thursday night when the Super Bowl champion Kansas City Chiefs host the Baltimore Ravens. For the 83rd consecutive year, the actual kickoff will be with the official, American-made Wilson Sporting Goods football.
The Chiefs have been a model of consistency, having appeared in the Super Bowl four times in the last five years. But the Wilson football and the Wilson Football Factory in Ada, Ohio, hold their own consistency record as the longest running partnership between a professional sports organization and a sporting goods supplier.
And it all takes place in a small village in rural Ohio, 69 miles southwest of Toledo.
The Wilson football is still manufactured by hand, the same way it has been done since the first year of production in 1941, when it was produced by the Ohio-Kentucky Leather Company in Chicago. In 1955, Wilson bought the Ohio-Kentucky Leather Company and moved the manufacturing to Ada.
There are not a lot of changes in the football manufacturing each year, but the Wilson Football Factory moved into a new facility this past May to modernize and increase its space to 80,000 square feet, up from 32,000 square feet. The new building hosts guided tours during the week, and even has a small museum documenting the history of the Wilson football.
But with the changes and growth, most everything continues to stay the same in the manufacturing of the renowned “pigskin.”
“Everything absolutely is still done by hand,” said Wilson Football manufacturing engineer Mike Springer. “There is not a lot of automation here. We added some conveyor belting but every ball is still sewn by hand, turned by hand, laced by hand, and cut by hand by the workforce on the floor.”
A crew of 140 craftspeople work on the production floor, an increase of 20 employees since the move to the new factory, which conveniently is located right next door to the old plant. The production floor workers are members of Local 1385 of the Chicago and Midwest Regional Joint Board of Workers United.
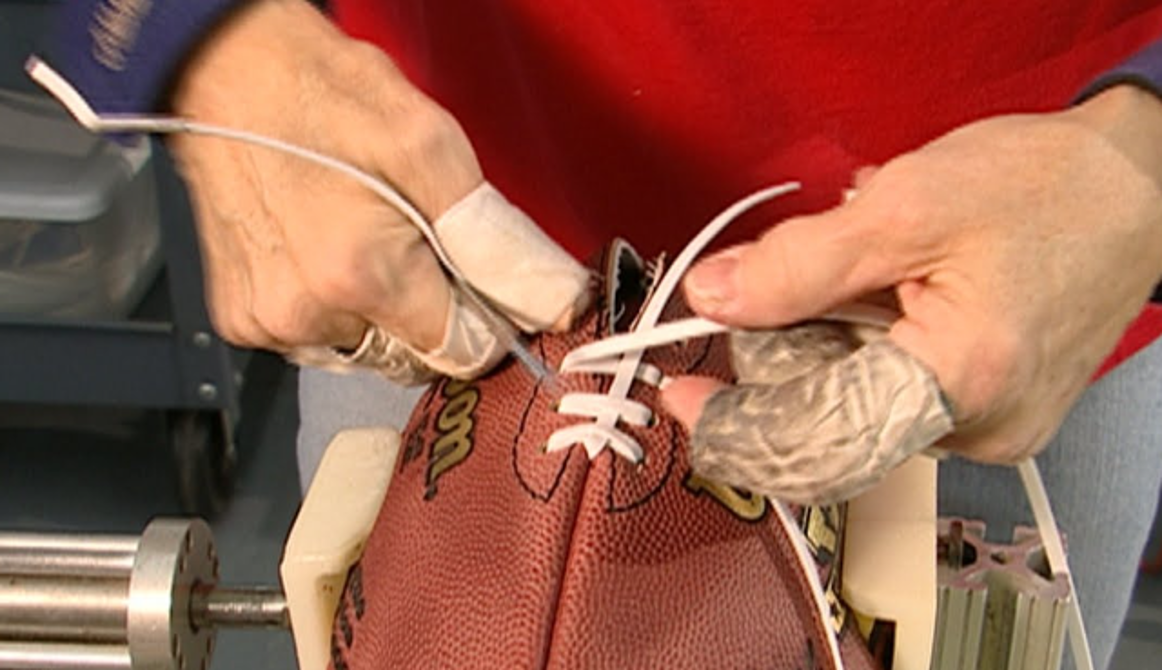
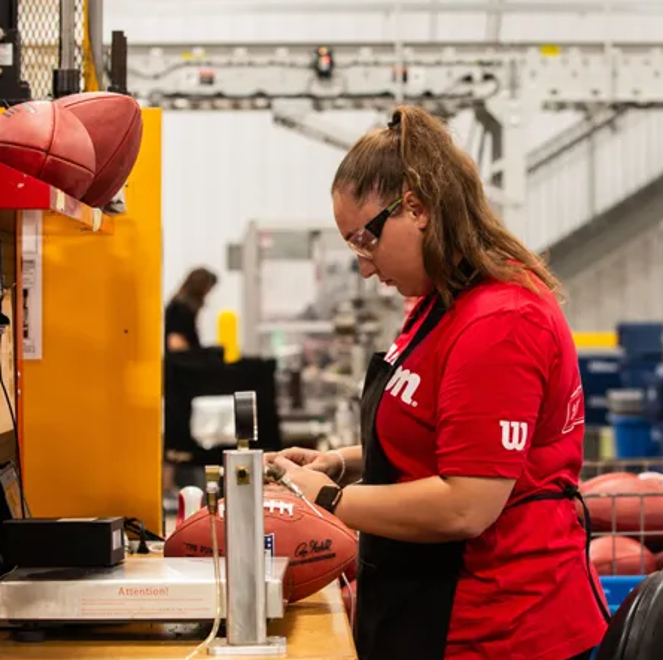
And today, the Football Factory continues to hire new football manufacturing talent.
“In the old facility, we were producing around 2,500 footballs a day, and we would like to get up to about 3,000 a day over here,” Springer said. “When we post a job opening, we have about 20 to 30 people apply for it.
“We have filtered air and a much cleaner environment for the employees, and they are extremely happy with it. We can produce more footballs, increase production, and increase production on not just leather footballs but on custom footballs and collaborations.”
In the manufacturing of the footballs, the first step is cutting the leather which comes from Horween Manufacturing in Chicago. Then, the graphics such as the Wilson moniker and the NFL football’s nickname “The Duke” are stamped onto the ball.
When graphic work is complete, workers sew the ball from the inside out and turn it right side out. They then put the bladder in the ball and lace it. It is then molded to give it its final shape.
After inspection, the balls are shipped to the respective teams, and everything is officially underway for another American-made football season.
“We supply the NFL with 27,000 footballs a year, and they are already made for the season,” Springer said. “Each team gets 780 footballs for the season, and the equipment managers for the teams have those balls already for the season.”
The Wilson Football Factory makes five different sized footballs for use by kids and professionals alike. It ranges from Pee Wee size; footballs for players in fourth through six grades; a junior high school model; one for high school and college (which are the same size); and the NFL size ball, which is also used in the Canadian Football League.
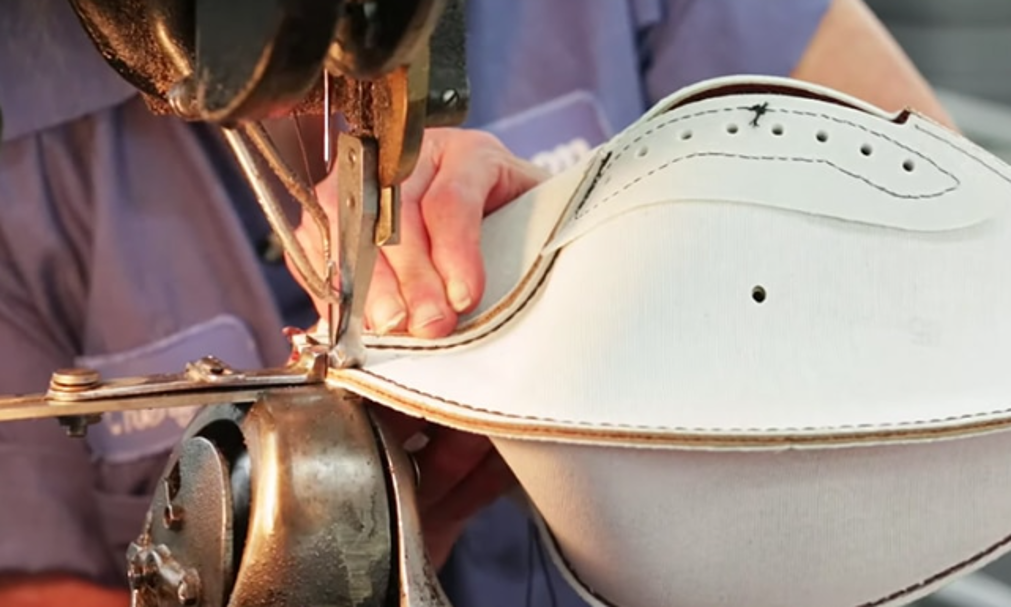
But a special production run takes place after the Super Bowl teams have been determined.
“We actually have a small group of individuals come in on Sunday night and watch the NFC and AFC championship games, and as soon as we know that night who the winners of those games are, we’ll start stamping team names on the footballs,” Springer said. “Each team will get 108 balls, 54 on that Monday and 54 on Tuesday. The equipment managers will have almost two weeks to prep the balls for the quarterbacks to be used in the Super Bowl. It’s always something special around here.”
There is one special modernization of the footballs that most fans do not know about and cannot see on close visual inspection. Each NFL football contains a sensor that is sewn into the bladder of the ball that can track vital statistical information in real time.
So, when the television cameras turn to the press box and we get a glimpse of coaches pouring over their laptop computers, it is not all about the Xs and Os of play calling.
“All the players have sensors on them as well under their shoulder pads,” Springer said. “The pylons have sensors on them, the chain gangs have sensors. It is used for tracking the ball on the field and player performance.
“You can see every route run by a running back, every route run by a receiver, every throw from the quarterback. The sensor is sending data from inside the football to the stadium so we can track that ball and its movement on the field.
“If you go to next gen stats on NFL.com, you can see the fastest player in the NFL, the farthest ball thrown and track field goal kickers. Even the Dallas Cowboys kicker in one preseason game kicked a 66-yard field goal and the data from the sensor said based on the trajectory and speed of that ball that it would have been good from 72 yards.”
The sensors, supplied by Zebra Technologies in Illinois, are a high-tech take on the old-fashioned hands-on manufacturing of the NFL footballs.
“They can actually use it for coaching for different route running and the quarterback can use it for recognizing defenses,” Springer added. “The RPM is a critical measurement for a quarterback. So, if you have Patrick Mahomes throws or Tom Brady’s, you can see how fast they are spinning the ball, how fast they are throwing the ball, the trajectory of the ball and how consistent they are.
“So many of these passing plays in the NFL, a lot of times the quarterback is throwing the ball, and the receiver has not even turned his head to look for it. It helps with the timing patterns and how consistent you throw that ball.”
Click here to schedule a tour of the Wilson Football Factory in Ada, Ohio.