Turning is a foundational process in machining, integral to manufacturing precision components that meet the rigorous demands of various industries. This extensive guide explores every facet of turning, from basic principles to advanced techniques and future trends, providing a comprehensive understanding for both novices and seasoned professionals in the field.
What is Turning?
Definition
Turning is a subtractive machining process where a workpiece is rotated on a lathe, while a cutting tool removes material to create cylindrical shapes. This technique is primarily utilized for producing parts like shafts, bushings, and other round objects. The lathe’s ability to rotate the workpiece allows for precise shaping and finishing, making turning one of the most widely used processes in manufacturing.
Importance of Turning in Machining
Turning is vital in numerous sectors, such as:
- Automotive: Creating engine components, transmission parts, and various fittings.
- Aerospace: Manufacturing high-precision components that require stringent quality standards.
- Manufacturing: Producing a wide array of mechanical components for various machines.
The versatility and efficiency of turning enable manufacturers to produce high-quality parts quickly and at scale, which is crucial in today’s fast-paced industrial environment.
Types of Turning Operations
Turning encompasses several specific operations, each designed to achieve distinct outcomes. Understanding these operations helps in selecting the appropriate technique for a given task.
1. Facing
Process: Facing involves cutting the end of the workpiece to create a flat surface. This operation is typically the first step in preparing a workpiece for further machining, ensuring that it is correctly aligned.
Applications: Facing is used in various settings, including:
- Initial preparation of a workpiece before further operations.
- Creating a flat surface for mounting or assembly.
Techniques and Considerations:
- Tool Selection: Typically, a flat-ended tool or a rounded tool may be used depending on the desired finish.
- Feed Rate: Careful selection of feed rate is important to prevent chatter and achieve a smooth surface.
- Depth of Cut: Usually shallow to prevent tool wear and maintain accuracy.
2. Straight Turning
Process: Straight turning reduces the diameter of the workpiece along its length, producing cylindrical sections.
Applications: Commonly used for manufacturing:
- Shafts: Essential components in motors and machines.
- Pins: Used in mechanical assemblies.
Techniques and Considerations:
- Cutting Speed: Should be optimized based on the material to balance efficiency and tool life.
- Tool Path: A straight tool path is essential for maintaining consistent diameter along the length of the part.
3. Taper Turning
Process: Taper turning involves creating a conical shape by gradually reducing the diameter of the workpiece. This is often achieved by adjusting the position of the tailstock or by using a taper attachment.
Applications: Useful for applications that require:
- Fitting parts together: Ensuring proper alignment in assemblies.
- Producing conical shapes: Necessary for specialized components like tool holders.
Techniques and Considerations:
- Angle Adjustment: The angle of taper can be set using the lathe’s tailstock or by programming CNC lathes.
- Depth Control: It is important to control the depth of cut and feed rate to achieve the desired taper without over-cutting.
4. Contour Turning
Process: Contour turning follows a specified path to create curved profiles on the workpiece. This operation is essential for producing non-linear shapes.
Applications: Employed in industries requiring:
- Decorative elements: Components that have aesthetic or functional curves.
- Complex geometries: Parts that must meet specific design requirements.
Techniques and Considerations:
- CNC Utilization: CNC lathes are often employed to program complex paths with high precision.
- Tool Selection: Appropriate tools with the right geometry are critical to achieve smooth contours.
5. Thread Cutting
Process: This operation creates internal or external threads, using either single-point tools or specialized thread-cutting tools.
Applications: Critical for producing:
- Fasteners: Bolts, nuts, and screws that hold components together.
- Mechanical assemblies: Where threaded components must fit precisely.
Techniques and Considerations:
- Tool Design: The geometry of the cutting tool is crucial for achieving the correct thread profile.
- Machine Settings: Accurate adjustments to spindle speed and feed rate are essential for quality threads.
6. Boring
Process: Boring enlarges existing holes in a workpiece and can achieve high precision. It often follows drilling to reach tighter tolerances.
Applications: Commonly used for:
- Adjusting hole sizes: Ensuring parts fit together correctly.
- Enhancing surface finishes: Achieving smoother interior surfaces.
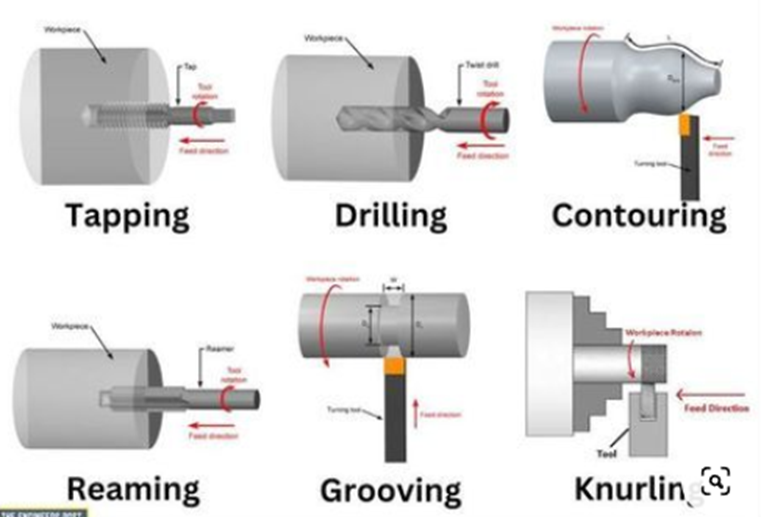
Techniques and Considerations:
- Tool Selection: Boring bars must be selected based on the material and desired hole diameter.
- Stability: Ensuring the workpiece is stable during boring is essential for maintaining precision.
Tools and Materials in Turning
The effectiveness of a turning operation largely depends on the cutting tools and materials used. The right tool choice can significantly impact efficiency, surface finish, and overall part quality.
Turning Tools
1. Tool Types
- Single-Point Cutting Tools: These tools have one cutting edge and are commonly used for general turning operations. They are versatile and can be used for facing, straight turning, and taper turning.
- Multi-Point Cutting Tools: Featuring multiple cutting edges, these tools are typically employed for threading and similar tasks, improving material removal rates.
2. Tool Materials
- High-Speed Steel (HSS): Known for its toughness and versatility, HSS is suitable for a wide range of materials and applications. HSS tools are often used for general-purpose machining due to their good wear resistance.
- Carbide: Harder and more wear-resistant than HSS, carbide tools are ideal for high-speed operations and can significantly increase productivity. These tools are suited for tougher materials and longer production runs.
- Ceramics: These tools are best for machining hard materials and can withstand high temperatures. However, they are more brittle and less forgiving in terms of tool setup. Ceramic tools excel in high-speed applications but require careful handling.
- Cubic Boron Nitride (CBN): This superhard material is suitable for machining hardened steel and offers excellent wear resistance. CBN tools are often used in finishing operations where surface integrity is critical.
3. Tool Geometry
Understanding tool geometry is essential for optimizing performance:
- Rake Angle: Influences cutting efficiency, chip flow, and the surface finish of the part. A positive rake angle can reduce cutting forces and improve chip removal, while a negative rake angle provides better edge strength for harder materials.
- Relief Angle: Prevents friction between the tool and the workpiece, allowing for smoother cutting action and reducing wear. The right relief angle is crucial for minimizing tool wear and maximizing tool life.
- Cutting Edge Geometry: The shape of the cutting edge affects how the tool interacts with the material, impacting the quality of the cut and the tool’s lifespan. Different applications may require varying edge shapes, such as sharp edges for softer materials or rounded edges for tougher materials.
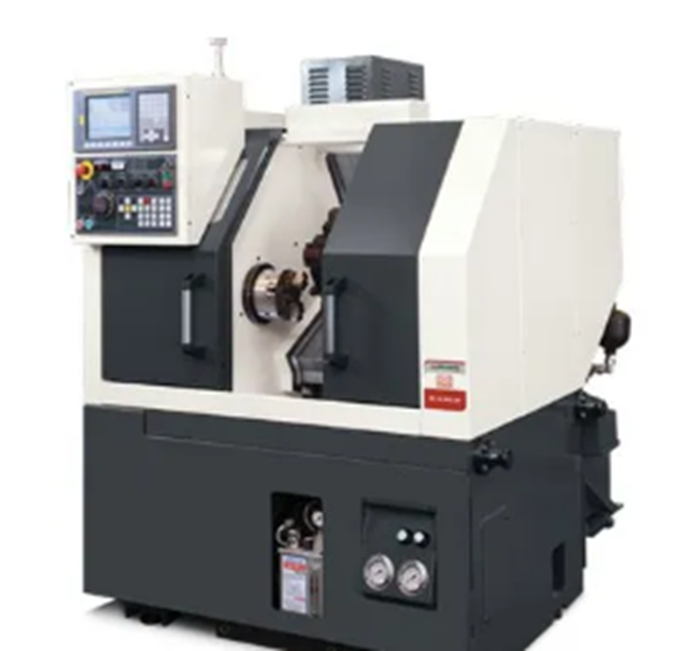
Tool Coatings
Modern cutting tools often feature specialized coatings to enhance performance:
- Titanium Nitride (TiN): This gold-coloured coating improves hardness and reduces friction, extending tool life and improving surface finish.
- Titanium Carbonitride (TiCN): This coating provides enhanced wear resistance, particularly useful in dry machining applications.
- Diamond Coatings: These are used for machining non-ferrous materials, offering exceptional hardness and low friction.
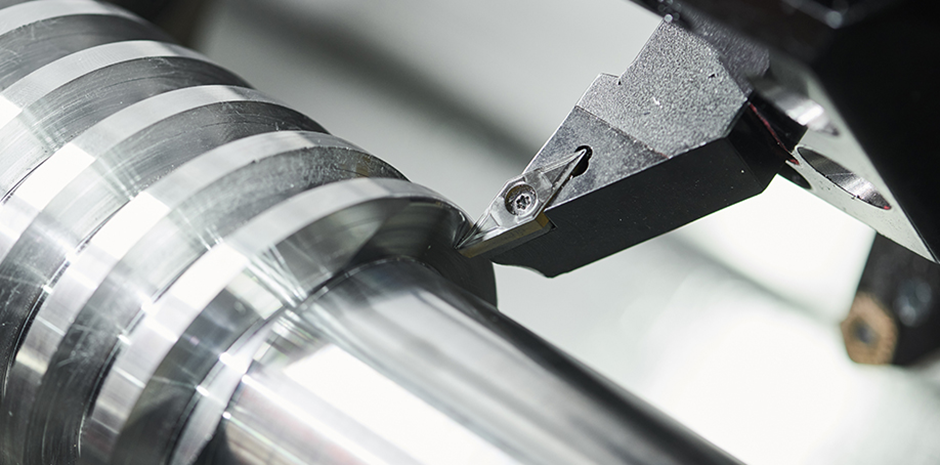
Machining Parameters in Turning
Optimizing the following parameters is essential for improving efficiency and quality in turning operations:
1. Cutting Speed
Cutting speed refers to the speed at which the cutting edge engages the workpiece, usually measured in surface feet per minute (SFM) or meters per minute (MPM). The optimal cutting speed varies based on factors such as:
- Material type: Different materials require different speeds; harder materials generally require lower cutting speeds to prevent excessive tool wear.
- Tool material: Harder tool materials can often handle higher speeds, allowing for more aggressive machining.
2. Feed Rate
The feed rate is the distance the cutting tool advances per revolution of the workpiece. It is a crucial parameter that affects:
- Material removal rate: A higher feed rate can increase productivity but may sacrifice surface finish quality.
- Surface finish: A slower feed rate usually results in a finer surface finish, as the tool spends more time on each area of the material.
3. Depth of Cut
Depth of cut refers to the thickness of material removed in a single pass. It influences both machining efficiency and tool wear. Adjusting this parameter can help balance:
- Tool life: Deeper cuts may increase wear on the tool, while shallower cuts can prolong tool life.
- Machining time: A deeper cut can reduce overall machining time but may require more robust tooling and machine capabilities.
4. Tool Path
The tool path refers to the trajectory that the cutting tool follows as it engages the workpiece. Optimizing the tool path is crucial for:
- Reducing cycle time: A well-planned tool path minimizes unnecessary movements and optimizes machining efficiency.
- Maintaining accuracy: Ensuring that the tool path is correctly programmed helps maintain tight tolerances and high-quality finishes.
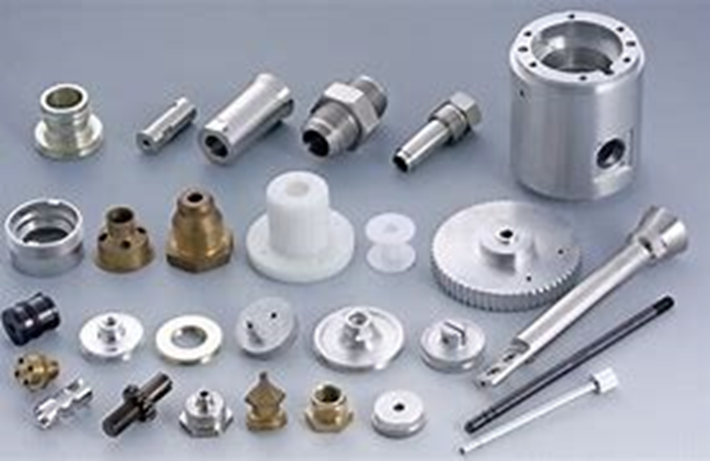
Work holding Techniques
Proper work holding is critical for ensuring accuracy and safety during turning operations. Various techniques are employed to secure the workpiece effectively.
1. Chucks
Chucks are devices that grip the workpiece during machining. Common types include:
- Three-Jaw Chucks: Automatically centre round parts and are widely used for their ease of operation. They provide reliable gripping for cylindrical components and are standard in many machine shops.
- Four-Jaw Chucks: Allow for holding irregularly shaped components and provide greater flexibility in work holding. Each jaw can be adjusted independently, making them suitable for complex or asymmetrical workpieces.
- Self-Centring vs. Independent: Self-centring chucks quickly centre round parts, while independent chucks offer more versatility for non-cylindrical shapes.
2. Collets
Collets are precision work holding devices that grip the workpiece tightly. They are particularly useful for high-precision applications where minimal runout is essential. Collets can accommodate various diameters, making them ideal for small-diameter workpieces.
3. Fixtures
Fixtures are custom-made devices designed to hold specific workpieces securely. They ensure consistent positioning and alignment throughout the machining process, enhancing productivity and precision.
- Design Considerations: Effective fixtures must account for part geometry, machining operations, and the need for easy access during loading and unloading.
- Quick Change Systems: These fixtures allow rapid setup changes, minimizing downtime and enhancing workflow efficiency.
Safety Considerations in Turning
Safety is paramount in any machining operation. Key safety practices include:
Safety Protocols
- Machine Guards: Protect moving parts to prevent accidents and injuries. These guards should be in place and checked regularly to ensure they provide adequate protection.
- Regular Maintenance: Conduct routine checks to ensure machines are functioning properly and to identify any potential issues before they become hazardous.
Personal Protective Equipment (PPE)
Wearing appropriate PPE is critical for ensuring safety in the workplace. Common PPE includes:
- Safety Glasses: Protect against flying debris, which can cause serious eye injuries. It’s essential that the lenses meet safety standards for impact resistance.
- Hearing Protection: Essential in noisy environments to prevent hearing loss. Workers should use earplugs or earmuffs, especially in environments exceeding 85 decibels.
- Gloves: Provide protection against cuts, although they should be chosen carefully to avoid entanglement with moving parts. Cut-resistant gloves are recommended for handling sharp tools or workpieces.
- Steel-Toed Boots: Protect feet from heavy objects that may fall during the machining process. Additionally, slip-resistant soles can help prevent falls in wet or oily environments.
Advanced Turning Techniques
With advancements in technology, turning has evolved to include several advanced techniques that improve efficiency and capability.
1. CNC Turning
Computer Numerical Control (CNC) turning machines have revolutionized the industry. These machines use computer programming to control the cutting tool’s movements, allowing for:
- Increased Precision: CNC lathes can achieve tighter tolerances and better repeatability than manual lathes, reducing errors in production.
- Complex Shapes: CNC technology enables the production of intricate designs that would be difficult or impossible to achieve manually, such as complex contours and varying diameters.
- Automation: CNC lathes can operate unattended for extended periods, enhancing productivity and reducing labour costs.
2. Live Tooling
Live tooling allows lathes to perform milling operations while the workpiece is rotating. This capability expands the lathe’s functionality, enabling it to:
- Reduce Setup Time: By performing multiple operations on a single machine, live tooling minimizes the need for part handling and setup, resulting in significant time savings.
- Improve Part Accuracy: Machining features such as slots or holes in a single setup enhances accuracy and reduces cumulative errors, which can occur with multiple setups.
3. Multi-Axis Turning
Multi-axis lathes can move in multiple directions simultaneously, allowing for complex geometries and intricate designs. This technology is essential for:
- Advanced Applications: Aerospace and automotive industries often require components with complex shapes that traditional lathes cannot achieve.
- Increased Efficiency: Multi-axis capabilities reduce machining time by allowing for more operations in a single setup, which is particularly beneficial for high-volume production runs.
4. Hybrid Machining
Combining traditional turning with additive manufacturing techniques, hybrid machining allows for the creation of complex geometries while maintaining the benefits of traditional machining. This approach can:
- Expand Design Possibilities: Designers can create shapes that would otherwise be impossible to machine conventionally.
- Reduce Material Waste: Additive processes can build up material only where needed, minimizing waste compared to traditional subtractive methods.
Applications of Turning in Various Industries
Turning plays a significant role in numerous industries, providing tailored solutions for a diverse range of applications.
1. Automotive Industry
In the automotive sector, turning is used to manufacture a variety of components, including:
- Engine Parts: Crankshafts, camshafts, and pistons, which require high precision to function effectively. These parts must withstand high pressures and temperatures, making accurate machining critical.
- Transmission Components: Gears and shafts that must meet strict tolerances for reliability and performance. The precise alignment of these components ensures smooth operation and longevity.
- Suspension Systems: Components such as control arms and bushings that require durability and precise dimensions for proper vehicle handling.
2. Aerospace Industry
The aerospace industry demands exceptional precision and quality, making turning essential for:
- Airframe Components: Structural elements that must withstand extreme conditions, such as high pressures and temperatures. These parts require rigorous testing and quality assurance.
- Engine Components: Parts that require lightweight yet strong materials, often produced using advanced alloys and composites. The ability to machine these materials accurately is critical for safety and performance.
- Landing Gear: Components that undergo significant stress and must be manufactured to stringent tolerances to ensure aircraft safety.
3. Medical Device Manufacturing
Turning is also pivotal in the production of medical devices, where precision and reliability are paramount:
- Surgical Instruments: Instruments such as scalpel handles, and drill guides must be manufactured with tight tolerances to ensure proper functionality and safety.
- Implants: Components like hip and knee replacements that require precise dimensions and smooth surfaces to ensure biocompatibility and longevity.
- Diagnostic Equipment: Parts used in imaging and diagnostic machines, where accuracy is essential for proper operation and results.
4. Electronics Industry
The electronics industry relies on turning for producing various components:
- Connectors: Components that require precise dimensions for reliable electrical connections.
- Heat Sinks: Machined parts that dissipate heat from electronic devices, requiring efficient thermal properties and precise surface finishes.
- Enclosures: Housing for electronic devices that must be both functional and aesthetically pleasing.
Future Trends in Turning
As technology continues to evolve, the field of turning is poised for significant advancements that will enhance capabilities and efficiency.
1. Smart Manufacturing
The integration of IoT (Internet of Things) technologies into machining processes enables real-time monitoring and data collection, leading to:
- Predictive Maintenance: Sensors can detect wear and tear on machines, allowing for timely maintenance and reducing downtime.
- Enhanced Decision Making: Data analytics can provide insights into production processes, helping manufacturers optimize operations and improve quality.
2. Automation and Robotics
The use of automated systems and robots in machining processes is increasing, leading to:
- Improved Productivity: Automation allows for continuous operation without human intervention, significantly increasing output.
- Consistent Quality: Robots can perform repetitive tasks with high precision, reducing human error and variability in production.
3. Sustainable Machining Practices
With growing concerns about environmental impact, the industry is focusing on sustainable practices, including:
- Energy Efficiency: Implementing energy-efficient machinery and processes to reduce consumption and minimize carbon footprints.
- Waste Reduction: Techniques such as recycling scrap materials and optimizing machining parameters to minimize waste generation.
- Coolant Management: Using biodegradable coolants and minimizing coolant usage to reduce environmental impact.
4. Advanced Materials
The introduction of new materials will continue to challenge traditional machining processes, requiring ongoing adaptations in tooling and techniques:
- Composite Materials: Increasingly used in industries such as aerospace and automotive, these materials require specialized tools and processes for effective machining.
- High-Strength Alloys: With applications in extreme environments, these alloys demand advanced machining techniques to achieve desired properties and performance.
Conclusion
Turning is a critical process in modern manufacturing, providing the foundation for producing high-quality, precision components across a wide range of industries. As technology continues to advance, the techniques, tools, and practices associated with turning will evolve, offering new opportunities for efficiency and innovation. By understanding the fundamentals of turning, manufacturers can better leverage this essential machining process to meet the challenges of today and tomorrow.
Stay Tuned for Next Month!
In our next topic, we will dive into the latest advancements in CNC turning technology and how they are shaping the future of machining.
You Tube channel link- https://www.youtube.com/@CNC_Guru_Tech_Center
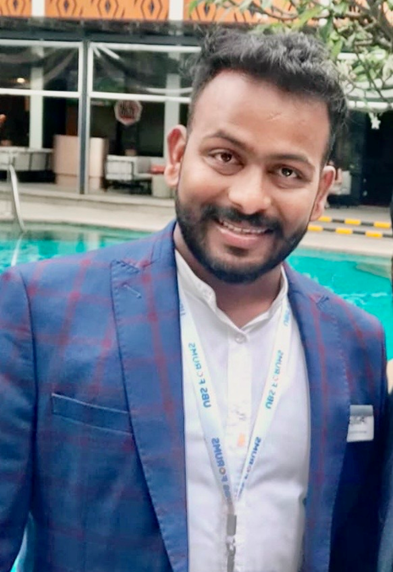
S. Jagnnath
Sr. Instructor -Advance Manufacturing.
TATA Indian Institute of skills, Mumbai
I hold a B. Tech in Production Engineering from SGGSIE&T Nanded and have over 10 years of experience in the training sector, specializing in CNC skill development initiatives. I’ve worked as an Application Engineer at Siemens Digital Experience Centre, Master Trainer at Bharat Forge, and Technical Training Manager at Godrej & Boyce. Additionally, I’ve served as a Subject Matter Expert at Phillips Machine Tools and as Associate Training Manager at Ace Micromatic. Currently, I am a Senior Instructor in Advanced Manufacturing at TATA Indian Institute of Skills in Mumbai. I also run a CNC training YouTube channel with over 80K subscribers.